Bare Pipe :
A pipe is considered bare if it does not have a coating adhered to it. Typically, once rolling is complete at the steel mill, the bare material is shipped to a location designed to protect or coat the material with the desired coating (which is determined by the ground conditions of the location the material is being used). Bare pipe is the most common type of pipe used in the piling industry and it is often put into the ground for structural use. Although there are no concrete studies to suggest that bare pipe is more mechanically stable than coated pipe for piling applications, bare pipe is the norm for the structural industry.
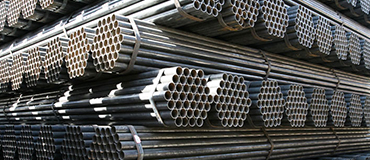
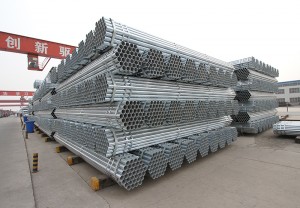
Galvanizing Pipe :
Galvanizing or galvanization is one of the most popular types of steel pipe coating. Even when the metal itself has a number of excellent properties when it comes to corrosion resistance and tensile strength, it needs to be further coated with zinc for a better finish. Galvanizing can be done in a number of ways, depending on the availability of the method. The most popular technique, however, is hot-dip or batch dip galvanizing which involves a submersion of a steel pipe into a bath of molten zinc. A metallurgical reaction formed by the steel pipe alloy and the zinc creates a finish on the metal’s surface that provides a corrosion-resistant quality never present on the pipe before. One other advantage of galvanizing is the cost benefits. As the process is simple and doesn’t require too many secondary operations and post-processing, it has been the go-to choice for many manufacturers and industries.
FBE - Fusion Bonded Epoxy Powder Coating Pipe :
This pipe coating provides excellent protection for small to large diameter pipelines with moderate operating temperatures (-30C to 100C). Its application is most often used for oil, gas, or waterworks pipelines. The excellent adhesion allows long term corrosion resistance and protection of the pipeline. FBE can be applied as a dual layer which provides strong physical properties that minimize damage during handling, transportation, installation, and operation.
Single Layer Fusion Bonded Epoxy Anticorrosive Pipe : Electrostatic power coating;
Double Layer Fusion Bonded Epoxy Anticorrosive Pipe : Fistly bottom epoxy powder, and Then epoxy powder Surface.
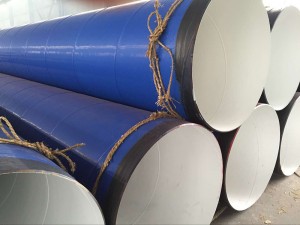
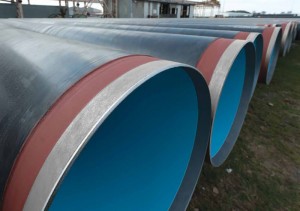
3PE Epoxy Coating Pipe :
3PE Epoxy coated steel pipe is with 3 layer coatings, first FBE coating, middle is adhesive layer, outside polyethylene layer. 3PE coating pipe is another new product developed on the FBE coating basis since 1980s, which contains adhesives and PE(polyethylene) layers. 3PE can strengthen the pipeline’s mechanical properties, high electrical resistance, waterproof, wearable, anti-aging.
For The first layers is fusion bonded epoxy, which thickness is larger than 100μm. (FBE>100μm)
The second layer is adhesive, which effect is binding epoxy and PE layers. (AD: 170~250μm)
The third layers is PE layers which is polyethylene have advantages to anti-water, electrical resistance and anti mechanical damage. (φ300-φ1020mm)
Therefore, 3PE coating pipe integrated with the advantages of FBE and the PE. Whichg more and more widely used in buried pipeline’s transporting of water, gas and oil.
Post time: Mar-03-2022