304/304L stainless seamless steel pipe is one of the very important raw materials in the manufacture of stainless steel pipe fittings. 304/304L stainless steel is a common chromium-nickel alloy stainless steel with good corrosion resistance and high temperature resistance, which is very suitable for the manufacture of pipe fittings.
304 stainless steel has good oxidation resistance and corrosion resistance, and can maintain the stability and strength of its structure in a variety of chemical environments. In addition, it also has excellent processing performance and toughness, which is convenient for cold and hot working, and can meet the manufacturing requirements of different pipe fittings.
Stainless steel pipe fittings, especially seamless pipe fittings, have high requirements for materials and need to have good sealing and pressure resistance. 304 stainless seamless steel pipe is often used to manufacture various pipe fittings due to its high strength, corrosion resistance and smooth inner surface, such as elbows, tees, flanges, large and small heads, etc.
In short, 304 stainless seamless steel pipe plays an important role in the manufacture of stainless steel pipe fittings, they provide excellent performance and reliable quality, and provide an important guarantee for the safe operation and durability of pipe fittings.
Therefore, before leaving the factory in the production process of raw materials, it must undergo repeated tests and must meet the standard requirements for the production of pipe fittings. Here are some performance check methods of 304/304L stainless seamless steel pipe.
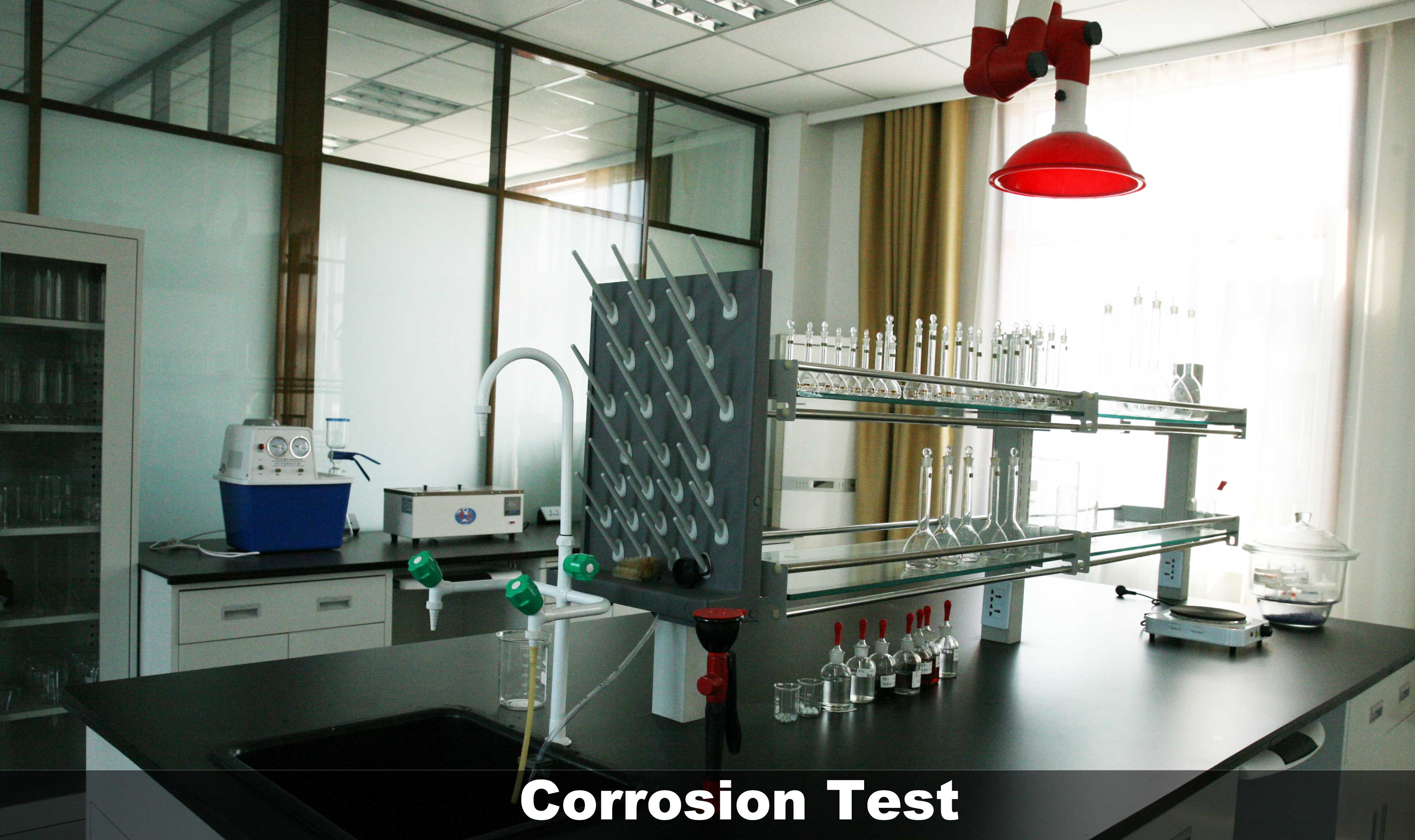
01.Corrosion testing
304 stainless seamless steel pipe should be subjected to corrosion resistance test according to the standard provisions or the corrosion method agreed by both parties.
Intergranular corrosion test: The purpose of this test is to detect whether a material has a tendency to intergranular corrosion. Intergranular corrosion is a type of localized corrosion that creates corrosion cracks at the grain boundaries of a material, eventually leading to material failure.
Stress corrosion test: The purpose of this test is to test the corrosion resistance of materials in stress and corrosion environments. Stress corrosion is a highly dangerous form of corrosion that causes cracks to form in areas of a material that are stressed, causing the material to break.
Pitting Test: The purpose of this test is to test the ability of a material to resist pitting in an environment containing chloride ions. Pitting corrosion is a localized form of corrosion that creates small holes on the surface of the material and gradually expands to form cracks.
Uniform corrosion test: The purpose of this test is to test the overall corrosion resistance of materials in a corrosive environment. Uniform corrosion refers to the uniform formation of oxide layers or corrosion products on the surface of the material.
When performing corrosion tests, it is necessary to select appropriate test conditions, such as corrosion medium, temperature, pressure, exposure time, etc. After the test, it is necessary to judge the corrosion resistance of the material by visual inspection, weight loss measurement, metallographic analysis and other methods on the sample.
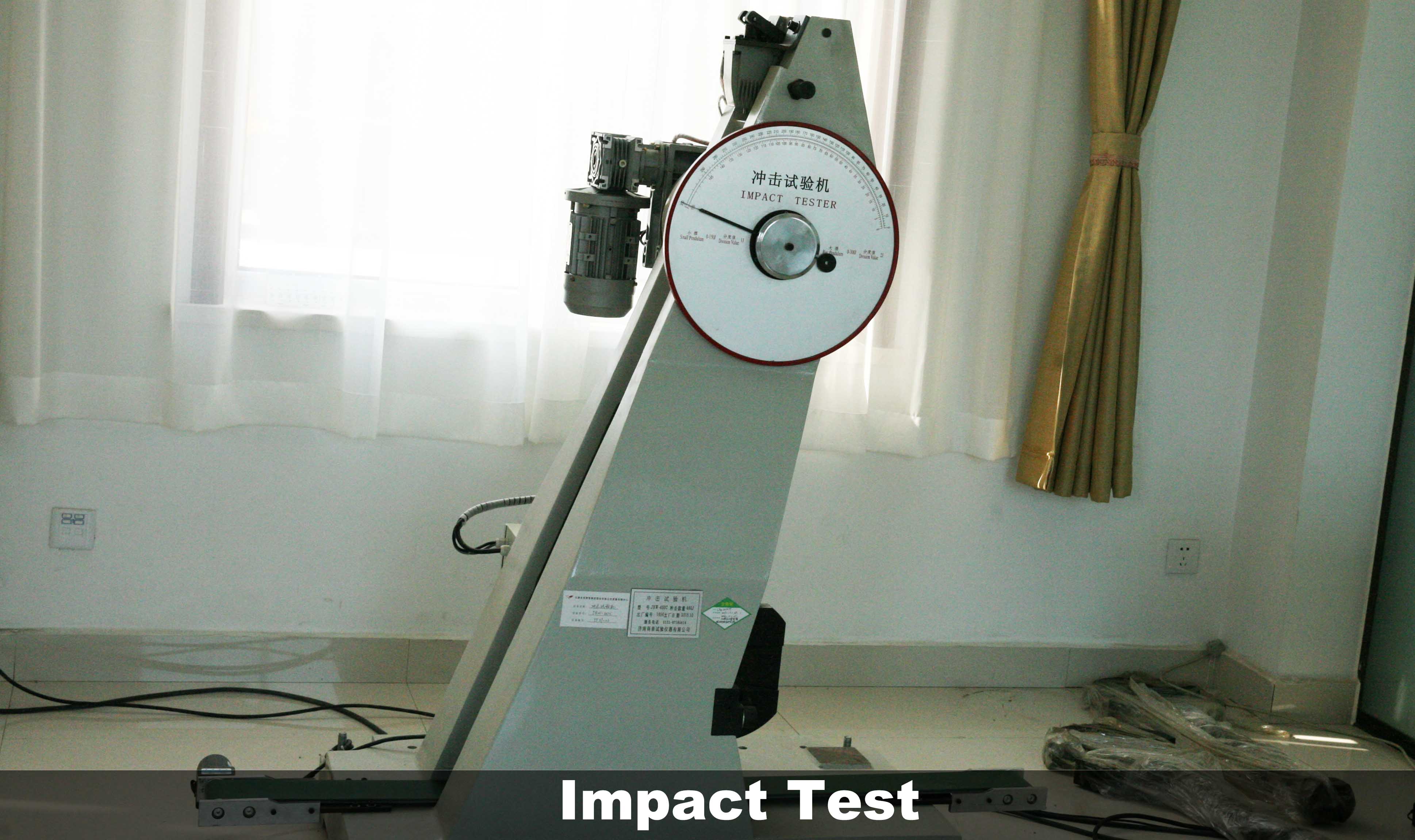
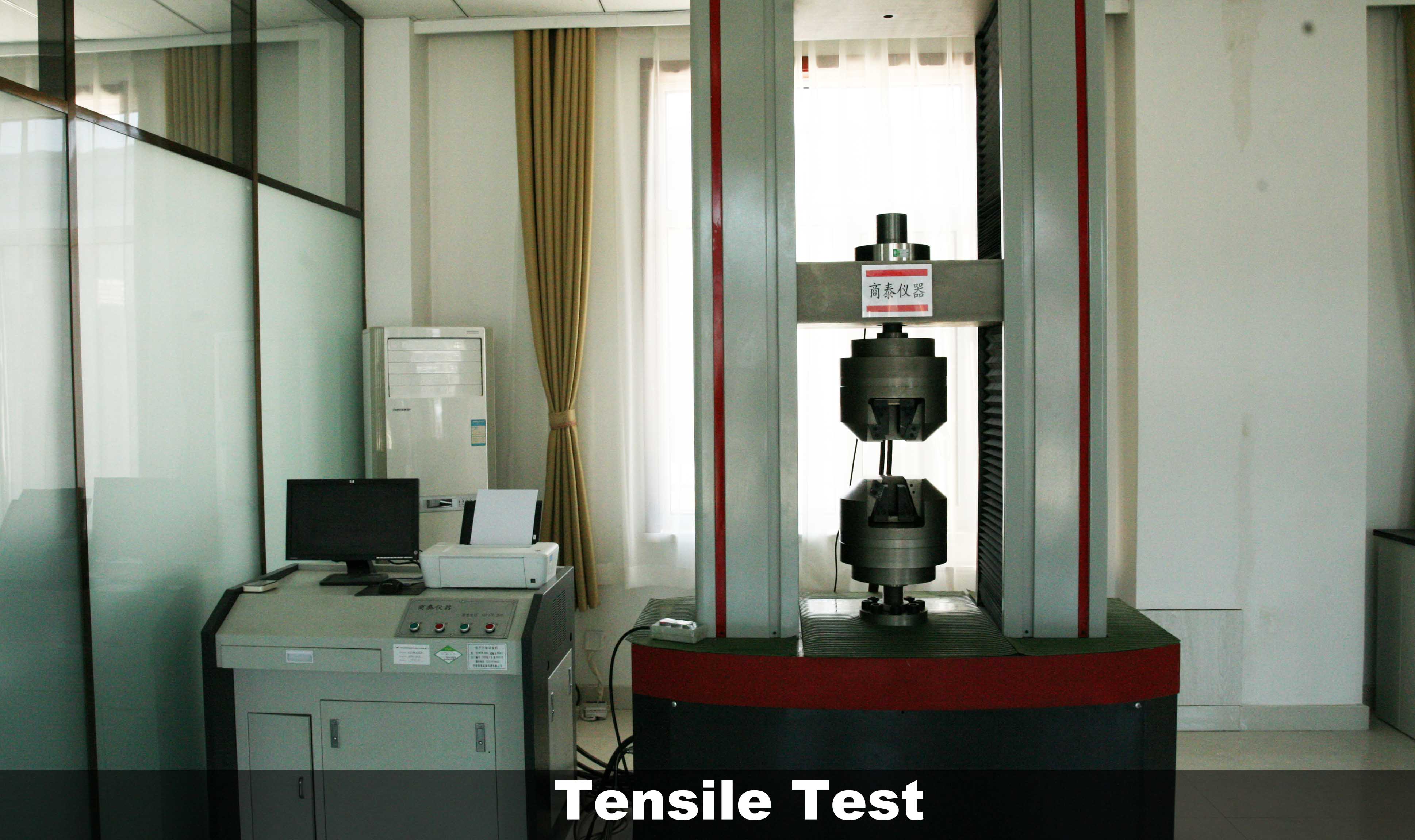
02.Inspection of process performance
Flattening test: detects the deformation ability of the tube in the flat direction.
Tensile testing: Measures the tensile strength and elongation of a material.
Impact test: Evaluate the toughness and impact resistance of materials.
Flaring test: test the resistance of the tube to deformation during expansion.
Hardness test: Measure the hardness value of a material.
Metallographic test: observe the microstructure and phase transition of the material.
Bending test: Evaluate the deformation and failure of the tube during bending.
Non-destructive testing: including eddy current test, X-ray test and ultrasonic test to detect defects and defects inside the tube.
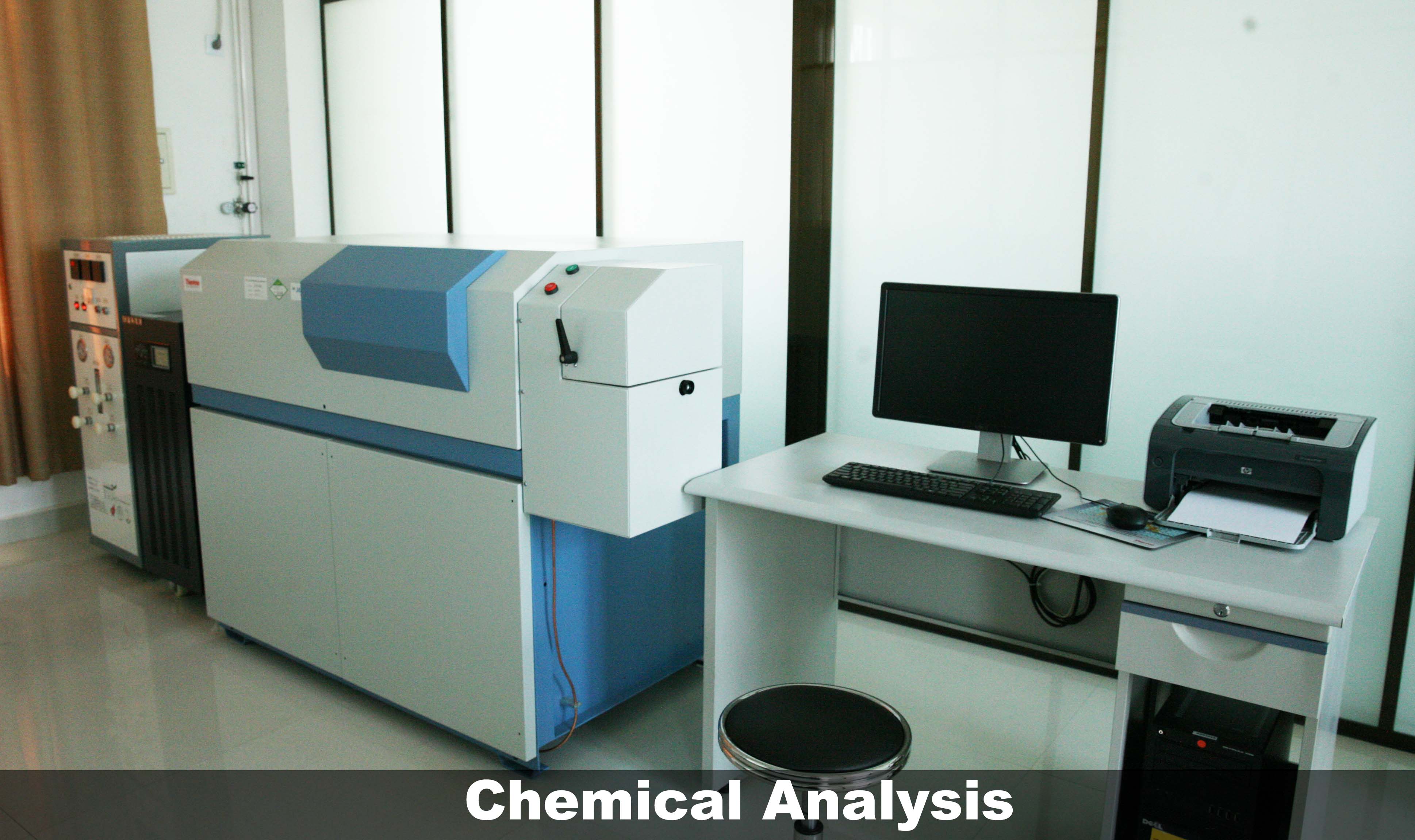
03.Chemical analysis
The chemical analysis of the material chemical composition of 304 stainless seamless steel pipe can be carried out by spectral analysis, chemical analysis, energy spectrum analysis and other methods.
Among them, the type and content of elements in the material can be determined by measuring the spectrum of the material. It is also possible to determine the type and content of elements by chemically dissolving the material, redox, etc., and then by titration or instrumental analysis. Energy spectroscopy is a quick and easy way to determine the type and amount of elements in a material by exciting it with an electron beam and then detecting the resulting X-rays or characteristic radiation.
For 304 stainless seamless steel pipe, its material chemical composition should meet the standard requirements, such as the Chinese standard GB/T 14976-2012 "stainless seamless steel pipe for fluid transportation", which stipulates various chemical composition indicators of 304 stainless seamless steel pipe, such as carbon, silicon, manganese, phosphorus, sulfur, chromium, nickel, molybdenum, nitrogen and other elements content range. When performing chemical analyses, these standards or codes need to be used as a basis to ensure that the chemical composition of the material meets the requirements.
Iron (Fe): Margin
Carbon (C): ≤ 0.08% (304L carbon content≤ 0.03%)
Silicon(Si):≤ 1.00%
Manganese (Mn): ≤ 2.00%
Phosphorus(P):≤ 0.045%
Sulfur(S):≤ 0.030%
Chromium (Cr): 18.00% - 20.00%
Nickel(Ni):8.00% - 10.50%
These values are within the range required by general standards, and specific chemical compositions can be fine-tuned according to different standards (e.g. ASTM, GB, etc.) as well as the manufacturer's specific product requirements.
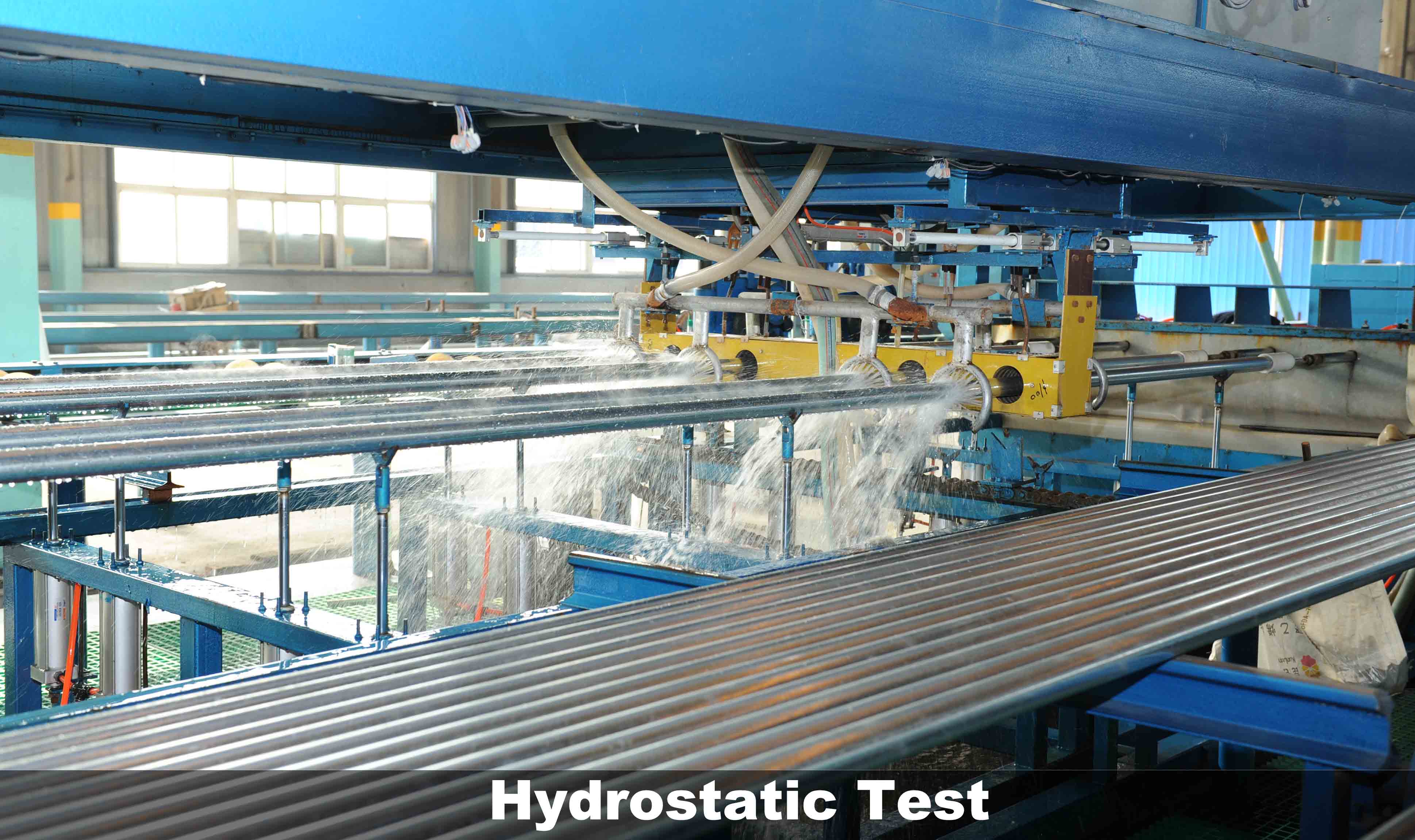
04.Barometric and hydrostatic test
The water pressure test and air pressure test of 304 stainless seamless steel pipe are used to test the pressure resistance and air tightness of the pipe.
Hydrostatic test:
Prepare the specimen: Select the appropriate specimen to ensure that the length and diameter of the specimen meet the test requirements.
Connect the specimen: Connect the specimen to the hydrostatic testing machine to ensure that the connection is well sealed.
Start the test: Inject water at a specified pressure into the specimen and hold it for a defined time. Under normal circumstances, the test pressure is 2.45Mpa, and the holding time cannot be less than five seconds.
Check for leaks: Observe the specimen for leaks or other abnormalities during the test.
Record the results: Record the pressure and results of the test, and analyze the results.
Barometric test:
Prepare the specimen: Select the appropriate specimen to ensure that the length and diameter of the specimen meet the test requirements.
Connect the specimen: Connect the specimen to the air pressure testing machine to ensure that the connection part is well sealed.
Start the test: Inject air at a specified pressure into the specimen and hold it for a defined time. Typically, the test pressure is 0.5Mpa, and the holding time can be adjusted as needed.
Check for leaks: Observe the specimen for leaks or other abnormalities during the test.
Record the results: Record the pressure and results of the test, and analyze the results.
It should be noted that the test should be carried out in a suitable environment and conditions, such as temperature, humidity and other parameters should meet the test requirements. At the same time, it is necessary to pay attention to safety when conducting tests to avoid unexpected situations during the test.
Post time: Jul-26-2023